Construction & Materials
Our goal is to build light but strong kayaks. The layups and materials were selected without a spreadsheet. That way it could never be a consideration, no compromises. Considerable effort was applied to find the right reinforcements to blend with the right resin systems. We consulted with a couple of highly trained composite engineers to evaluate the layup schedule. Careful attention to fabric selection and orientation of the weave ensures a boat that will achieve the full potential of every material selected. We are utilizing stitched reinforcements in high stress areas, as the fibers are straight as opposed to crimped in a woven fabric.
Innegra This “wonder fiber” has become a staple in the competition whitewater scene for a few years. Canoe manufacturers have adopted it as the replacement for Royalex when the manufacturer ceased production. It is also utilized by the Aerospace industry and Formula 1 race car builders. The kayak industry has been slow to adopt its use. We are using it in every layup for the ultimate strength to weight ratio.
Benefits-
-
Reduced weight
Increased damage tolerance
Increased impact resistance
Reduced maintenance
Incredible strength to weight ratio
Hydrophobic (doesn’t absorb moisture)
Dampens vibration
Disperses energy
Significantly reduces catastrophic failure.

Resin Systems

High quality materials and careful attention to detail, show clearly in the finished product. The layups and gelcoats were carefully selected to minimize print through. The result is a mirror finish in the gelcoat.
We use Vinylester (for fiberglass) and Epoxy (for carbon fiber) resins in our layups. The old technology Polyester can not match the strength of VE or Epoxy, so why use it. For the Carbon layups, Epoxy Infusion Resin is used. VE and PE resins do not bond well with carbon fiber. Epoxy maximizes the properties of carbon fiber and is the strongest resin available. Some manufacturers will still use the PE and VE resins with carbon to cut cost and be able to use a cheaper gelcoat system. Not here, we believe in using the right materials as a system for the best results.
Resin Infusion Process
Simply put, Resin Infusion produces the best resin to cloth ratio for the highest strength. We are using infusion as the standard construction method on all boats. Hand laid and vacuum bagged layups lack the strength of an infused layup because the higher resin content. Unsupported resin has no structural integrity and thus reduces the impact resistance and stiffness of a hand or vacuum bagged layup.
After the initial gel coat application has cured to a tacky state, the laminate layers are put in the mold dry. This allows time to carefully apply each layer and keeps cloth distortions minimal. There is no racing a curing pot of resin to hurry the process! Slow and methodical means the highest quality layup possible.
The consumable supplies are next to go in the mold. A layer of Peel Ply allows the removal of these consumables once the resin has cured. It also provides a smooth inner surface of the hull and deck. Flow media is next and controls the uptake of resin in the mold. It directs the resin throughout the mold ensures that it happens before the resin reaction occurs. Depending on temperature and catalyst ratio, a full infusion should happen within 15 minutes. The vacuum bag is the last component in the infusion process. It develops about 2,000 lbs of force per square foot of surface area. It compacts the layup and is the mechanism that draws in the resin and drives it into the reinforcement layers.
Once cured, the hull or deck are left in the mold and gently heated at least 12 hours to achieve a post cure. Unlike a hand layup, the part is fully cured and stable. They are ready to move on to the assembly stage.
The Skeg System
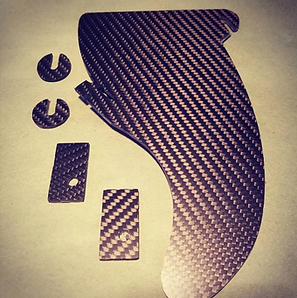


The skeg system was carefully designed for years of trouble free operation. The skeg is located off center to prevent it from being packed with debris when launching or landing. We selected the Karitek control for its simplicity and reliability. It is easily adjusted from in the cockpit to fine tune the skeg when necessary. The proprietary design of the skeg is unique. The blade is correctly sized to keep the boat on track when the conditions require, but small enough to be overcome by paddler input. No need to raise the skeg should you need to change direction. What makes this system unique is the orientation of the cable. It does not make a sharp bend like other systems. Instead it runs horizontally into the skeg box and is internally supported to prevent kinking should the skeg encounter something in the water. The operation is so smooth, it will kick up and push the control forward.
Hatches
Kajak Sport Performance hatches are made of real rubber. 100 % watertight hatch cover solution is created for the most demanding “expedition” use, when the cover is used in aberrant conditions and when the maximum reliability is essential. The cover is equipped with both inside and outside leash holders. Its material is extremely durable and long-lived. It is also fully UV-protected.
\The Day hatch configuration utilizes an “L-shaped” bulkhead. Large enough to handle your necessary supplies, and allows the aft compartment to handle longer items should you want to carry camping supplies along.
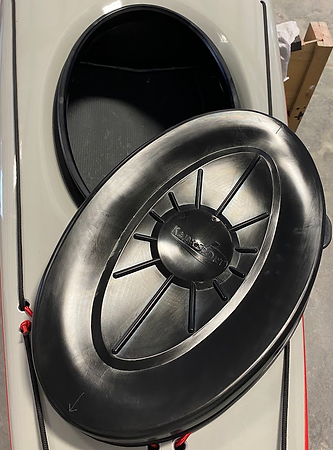